Custom Mold Maker: Elevating Standards in Metal Fabrication
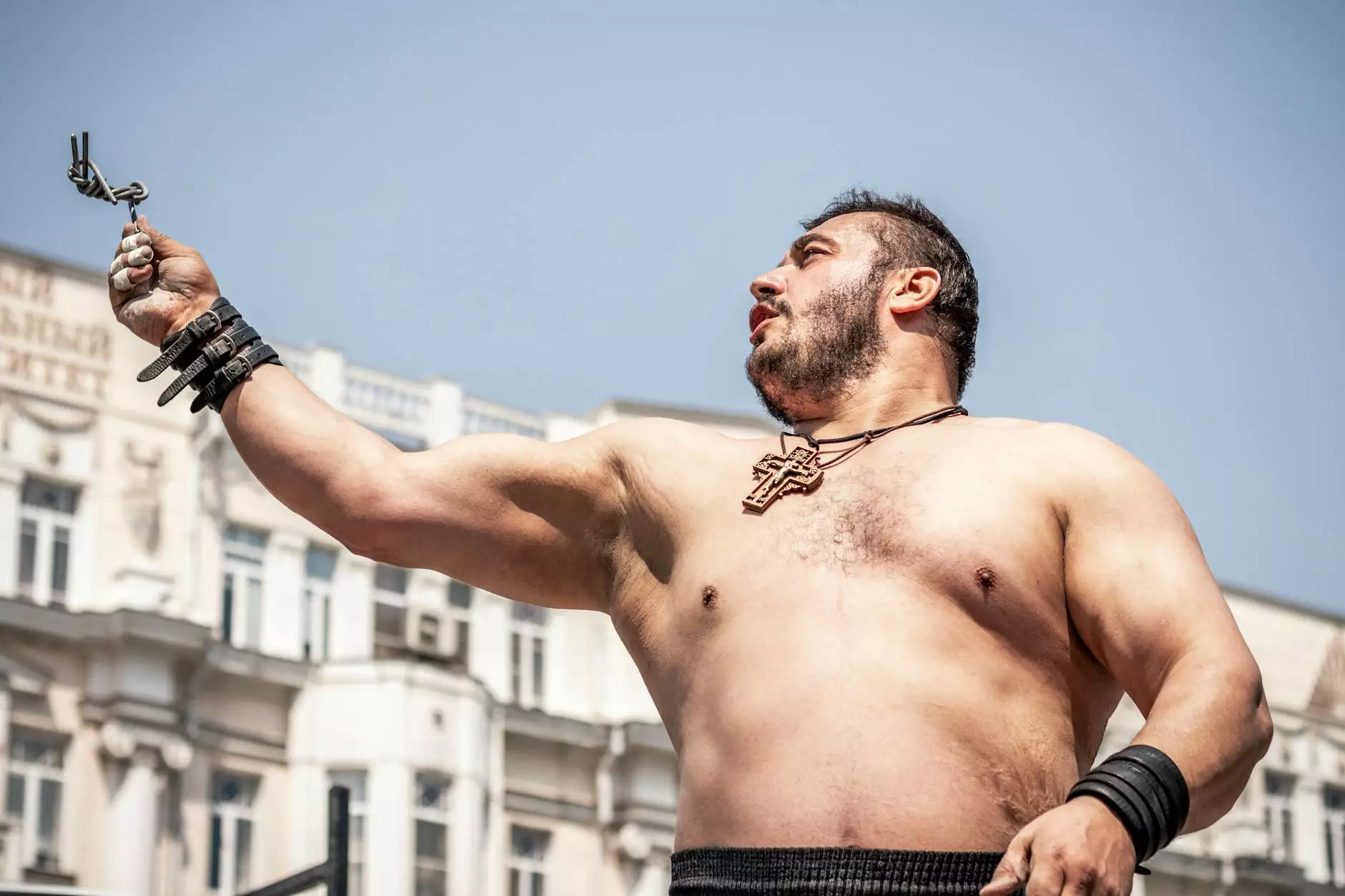
In the realm of manufacturing, the role of a custom mold maker is both pivotal and transformative. As industries increasingly demand precision and efficiency, the proficiency of those who create molds is paramount. This article dives deep into the intricacies of custom mold making and its significance for metal fabricators.
Understanding the Role of a Custom Mold Maker
A custom mold maker specializes in designing and producing molds that are tailored to the specific needs of a project. Molds are essential in various manufacturing processes, including injection molding, casting, and machining. They determine the shape and features of the final product, making precision is crucial for optimal functionality and aesthetics.
The Process of Custom Mold Making
The journey from concept to completion involves several meticulous steps:
- Design: Utilizing CAD (Computer-Aided Design) software, mold makers create detailed plans and prototypes of the mold. This phase is critical, as it ensures that every specification is met.
- Material Selection: Choosing the right materials for the mold is essential for durability and functionality. Common materials include steel, aluminum, and specialized alloys.
- Fabrication: The actual construction of the mold begins, utilizing various techniques such as CNC machining, electrical discharge machining (EDM), and manual fabrication.
- Testing and Quality Assurance: After fabrication, the mold is rigorously tested. This phase ensures that it meets industry standards and performs to its intended specifications.
- Final Adjustments: Based on testing feedback, adjustments may be made to enhance the mold's performance before it's final release.
Benefits of Working with a Custom Mold Maker
The advantages of collaborating with a professional custom mold maker are abundant:
- Precision: Custom molds are tailored specifically to your specifications, ensuring that the final product meets your exact needs.
- Cost Efficiency: Though custom molds may have a higher initial cost, they lead to savings in production efficiency and material wastage over time.
- Durability: High-quality molds made from superior materials ensure longevity, reducing the frequency and costs associated with replacements.
- Innovation: Skilled mold makers can implement the latest techniques and technologies, keeping you ahead of the competition.
- Expert Guidance: A seasoned custom mold maker offers invaluable insights, helping you choose the right materials and designs for your projects.
Applications of Custom Mold Making in Metal Fabrication
Custom mold makers play a significant role across various sectors in the metal fabrication industry. Their contributions can be seen in:
1. Aerospace Industry
The aerospace industry demands the highest levels of precision due to safety and performance standards. Custom molds can produce parts that meet stringent regulations while optimizing weight and strength.
2. Automotive Manufacturing
In automotive manufacturing, custom molds are used to create components that ensure functionality, safety, and aesthetic appeal. From dashboards to undercarriage parts, every element is critical.
3. Electronics Production
Electronics require molds that can accommodate intricate designs with tiny tolerances. A custom mold maker ensures that each piece fits seamlessly within larger systems.
4. Medical Equipment
Medical devices often require specialized molds that comply with health regulations. The precision in these molds can significantly affect the performance and safety of medical products.
Choosing the Right Custom Mold Maker
When selecting a custom mold maker, it is vital to consider several factors to ensure you partner with a quality provider:
1. Experience and Expertise
Look for mold makers with extensive experience in your specific industry. Their knowledge of industry standards and practices is invaluable.
2. Technology and Techniques
Advanced technology leads to better efficiency and precision. Ensure that the mold maker uses modern machinery and techniques.
3. Portfolio and References
Ask for examples of previous work and references from other clients. This will give you insights into their capabilities and reliability.
4. Certifications and Compliance
Validate that the mold maker holds necessary certifications. Compliance with industry regulations is non-negotiable, especially in critical sectors like aerospace and medical.
5. Customer Support and Communication
Effective communication is essential throughout the mold-making process. Evaluate how well potential partners engage with you.
The Future of Custom Mold Making
The landscape of mold making is continuously evolving with technological advancements. Noteworthy trends include:
1. Automation and Robotics
Automation is transforming the fabrication process, leading to higher efficiency and reduced production time. Robotics in mold making helps streamline operations.
2. 3D Printing Technologies
The integration of 3D printing in mold making allows for rapid prototyping and complex designs. This innovation facilitates testing and reduces lead times remarkably.
3. Sustainable Practices
The industry is leaning towards sustainable materials and processes. Custom mold makers are finding ways to reduce waste and enhance recyclability.
4. Enhanced Material Science
New materials, such as composites, are being developed for molds, offering remarkable durability and flexibility while maintaining reduced weight.
Conclusion: The Importance of a Skilled Custom Mold Maker
In conclusion, the significance of a custom mold maker in the metal fabrication process cannot be overstated. Their expertise not only fosters innovation but also ensures that industries meet their stringent quality and performance requirements. By investing in skilled mold makers, businesses can enhance their manufacturing capabilities, resulting in superior products that stand the test of time.
As the manufacturing landscape continues to evolve, embracing customized solutions and advanced technologies will be key for businesses seeking to maintain a competitive edge in an ever-changing market.