Concrete Batching Plant: Revolutionizing Construction Efficiency
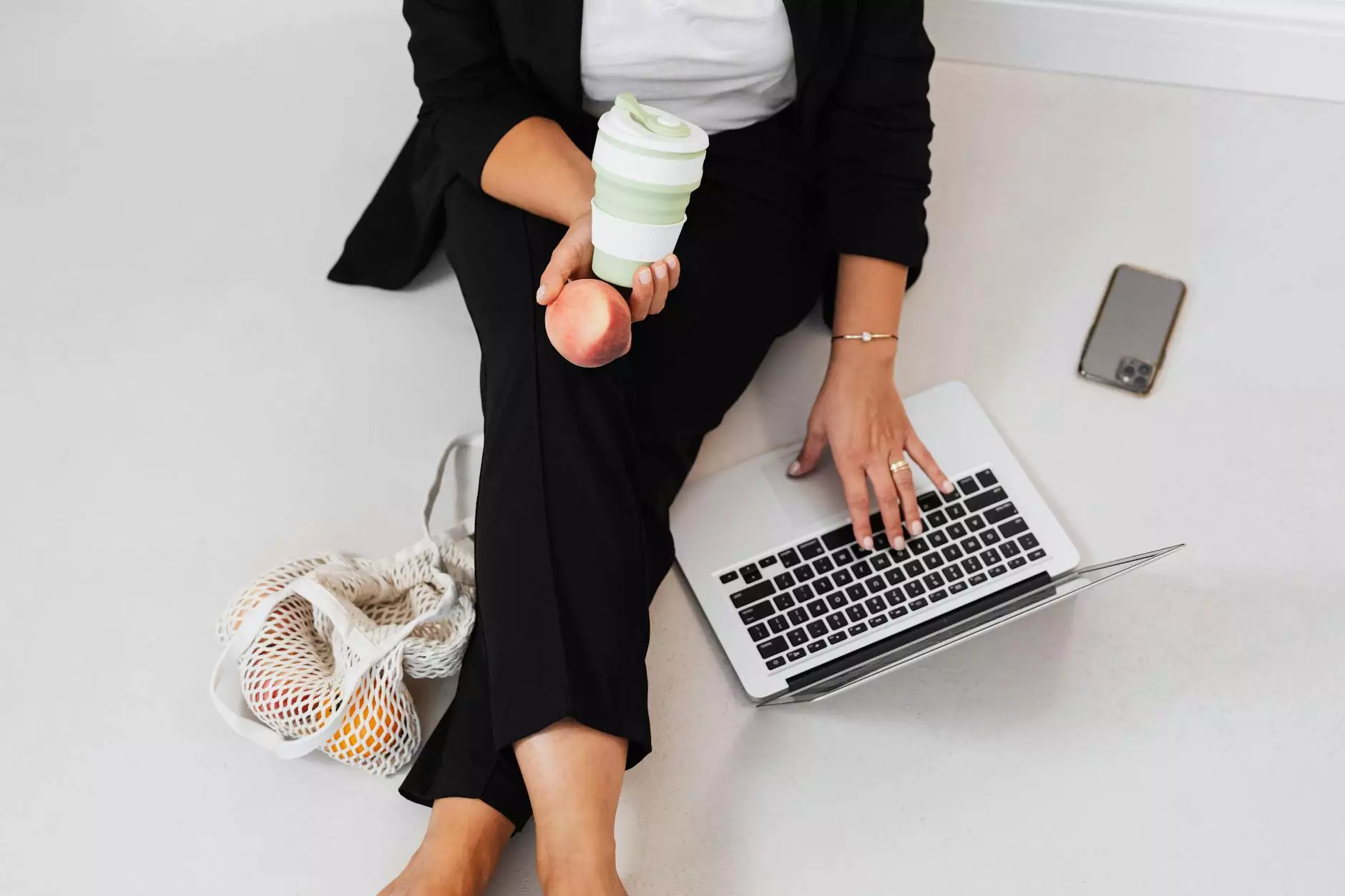
The construction industry is constantly evolving, and one of the most significant innovations that have emerged is the concrete batching plant. These plants are pivotal in streamlining the process of concrete production, ensuring efficiency, consistency, and quality. This article will delve deep into the various aspects of concrete batching plants, elucidating their importance and role in modern construction.
Understanding the Concept of Concrete Batching Plants
At its core, a concrete batching plant is a facility that combines a variety of ingredients to form concrete. The primary components include aggregates, cement, water, and sometimes admixtures. The production of concrete typically involves the following steps:
- Measurement: Precise measurement of each ingredient is crucial to achieving the desired concrete strength and workability.
- Mixing: Ingredients are mixed thoroughly to ensure a uniform consistency.
- Dispensing: The mixed concrete is then transferred to trucks or molds for transportation and setting.
Types of Concrete Batching Plants
Concrete batching plants come in various forms, tailored to meet different operational needs. Here are the primary types:
1. Stationary Concrete Batching Plants
Stationary plants are fixed installations, usually located near the construction site. They are ideal for large-scale projects that require a continuous supply of concrete. Characteristics include:
- Higher production capacity compared to mobile versions.
- Ability to accommodate bulk storage of raw materials.
- More complex and robust structure, allowing for advanced automation.
2. Mobile Concrete Batching Plants
Mobile plants are designed for flexibility, allowing them to be transported easily to various sites. Key benefits include:
- Portability: These plants can be set up and dismantled quickly, making them perfect for projects with fluctuating locations.
- Reduced transportation costs: By producing concrete on-site, you eliminate the need for transport logistics.
- Quick setup time: Ideal for remote locations where traditional batching plants are not feasible.
3. Continuous Concrete Batching Plants
These plants operate continuously, providing an uninterrupted production of concrete. This is particularly beneficial for large projects requiring high volumes of concrete. Features include:
- High efficiency: With ongoing production, workflow remains consistent.
- Less downtime: Continuous operation minimizes interruptions and maximizes productivity.
Benefits of Using Concrete Batching Plants
Employing a concrete batching plant can offer numerous advantages:
1. Enhanced Quality Control
One of the primary benefits of using a concrete batching plant is the ability to maintain strict quality control. By automating the mixing process, you can achieve consistent concrete quality, as all ingredients are measured accurately and mixed to perfection.
2. Increased Productivity
Concrete batching plants significantly increase productivity by allowing for a faster concrete production cycle. This optimizes project timelines and ensures that construction can proceed without delays due to concrete supply issues.
3. Cost-Efficiency
Although the initial investment in a concrete batching plant may be substantial, the long-term savings in labor, materials, and time can outweigh these costs. Additionally, producing concrete on-site reduces transportation expenses and minimizes the risk of material theft.
4. Environmental Benefits
Modern concrete batching plants are designed with environmental sustainability in mind. Many come equipped with systems to recycle water and aggregates, reducing waste. Furthermore, producing concrete on-site reduces the carbon footprint associated with transportation.
Key Components of Concrete Batching Plants
To understand the operation of a concrete batching plant, it's essential to know its key components. Here are the primary elements:
1. Aggregates Bins
These are storage units designed to hold various aggregates, including sand, gravel, and crushed stone. The bins can be configured to handle multiple types of aggregates, allowing for flexibility in concrete mix designs.
2. Mixer
The heart of any concrete batching plant is the mixer. There are different types of mixers used, including:
- Drum mixers: Ideal for small batches and quick mixing.
- Batch mixers: Used for larger volumes and produce high-quality concrete.
3. Weighing System
A precision weighing system ensures that all ingredients are measured accurately. This automation improves consistency and quality in the finished product, reducing human error.
4. Control System
Modern batching plants utilize advanced control systems for efficient operation. These systems allow for real-time monitoring and adjustments, ensuring optimal performance and quality assurance.
Choosing the Right Concrete Batching Plant
Selecting the appropriate concrete batching plant for your project involves several considerations:
1. Project Size and Scope
Determine the scale of your project and the volume of concrete needed. Larger projects will benefit from stationary plants, while smaller, dynamic projects may find mobile plants more advantageous.
2. Budget Constraints
Analyze your budget for both initial investment and operating costs. Consider not only the price of the plant but also long-term expenses, including maintenance and labor.
3. Site Conditions
Evaluate the site conditions where the plant will be located. Factors such as terrain, accessibility, and proximity to material sources will influence your decision.
Maintenance Tips for Concrete Batching Plants
Maintaining a concrete batching plant is essential for ensuring operational efficiency and longevity. Here are some maintenance tips:
1. Regular Inspections
Perform routine checks on all components, including mixers, weigh hoppers, conveyors, and control systems to catch potential issues early.
2. Cleaning
Concrete residue can accumulate and affect the operation. Regularly clean mixers, bins, and discharge chutes to avoid blockages and ensure consistent quality.
3. Lubrication
Ensure all moving parts are properly lubricated to reduce wear and tear. A well-lubricated plant operates more efficiently and longevity is enhanced.
4. Documentation
Keep thorough records of maintenance schedules, repairs, and inspections. This information can be invaluable in identifying patterns and preventing future problems.
Future Trends in Concrete Batching Technology
The evolution of concrete batching technology is ongoing, with exciting advancements making their way into the industry:
1. Automation and IoT
The integration of automation and the Internet of Things (IoT) is set to revolutionize concrete batching plants. These technologies facilitate real-time data analysis, predictive maintenance, and increased operational efficiency.
2. Sustainable Practices
As sustainability becomes increasingly critical in construction, batching plants are adopting eco-friendly practices, such as using recycled materials and optimizing energy consumption.
3. Smart Batching Systems
Smart batching systems that allow for remote monitoring and adjustments can enhance productivity and reduce human error, leading to significant improvements in concrete quality.
Conclusion
In conclusion, concrete batching plants play a fundamental role in the construction industry, enhancing quality, efficiency, and sustainability. Understanding the different types of plants, their components, and their benefits is crucial for any construction professional. As technology continues to advance, staying informed and adopting the best practices will ensure your projects are successful and meet the ever-growing demands of the market.
For more information on obtaining high-quality concrete batching plants, visit PolygonMach, where you'll find state-of-the-art solutions designed to elevate your construction capabilities.