The Essential Role of a Plastic Mold Maker in Modern Manufacturing
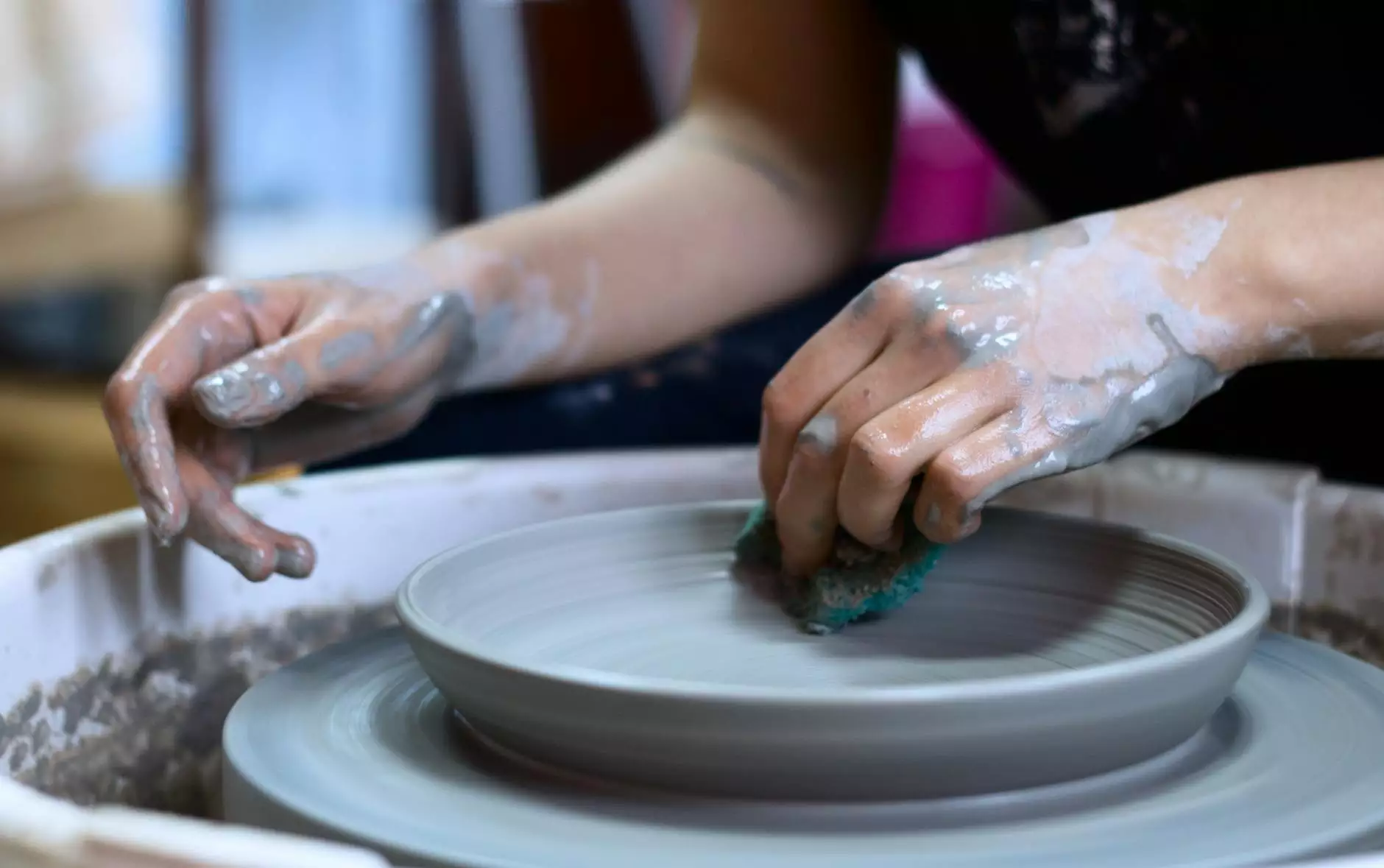
In today’s rapidly evolving manufacturing landscape, the importance of a plastic mold maker cannot be overstated. Whether it's in automotive parts, consumer goods, or complex dental devices, the precision and quality of plastic components are paramount. As a plastic injection mould manufacturer, we understand the intricate processes and skillsets that contribute to successful molding solutions.
What is a Plastic Mold Maker?
A plastic mold maker is a professional or organization that specializes in designing and producing molds used in the injection molding process. These molds are typically crafted from high-quality steel or aluminum and are engineered to create specific shapes and features of various plastic products. The expertise of a mold maker can directly impact the cost, efficiency, and quality of production. Without these skilled artisans, mass production of plastic items would be exceedingly challenging.
The Manufacturing Process of Plastic Molds
The journey from conceptualization to a finished product involves numerous steps:
- Designing the Mold: This initial step involves CAD software to create detailed designs that factor in aesthetics, functionality, and manufacturability.
- Material Selection: The choice of materials for the mold significantly affects durability and cost. Common choices are tool steel and aluminum.
- Machining: The mold is fabricated using CNC machining which offers precision cutting and shaping of the mold.
- Assembly: This step includes assembling the individual parts of the mold, ensuring perfect alignment and fit.
- Testing: A prototype mold is often created and tested to verify design functionality before full production.
- Production: Once validated, the molds are used in actual injection molding to produce the plastic components.
Advantages of Using Professional Plastic Mold Makers
Employing skilled plastic mold makers brings several significant advantages to manufacturing enterprises:
- Precision: High-quality molds produced by experts ensure that the final plastic products meet stringent quality controls.
- Cost Efficiency: Well-designed molds reduce production costs by minimizing waste and optimizing material usage.
- Shorter Lead Times: Professional mold makers typically have established processes that expedite production timelines.
- Technical Support: Experienced manufacturers, like those at hanking-mould.com, offer ongoing support and maintenance for the molds.
- Innovation: Expert mold makers are at the forefront of new technologies, including advancements in 3D printing for rapid prototype creation.
Types of Molds Produced by Plastic Mold Makers
The versatility of a plastic mold maker allows for the production of various types of molds, including:
- Injection Molds: Used for standard production of plastic products by injecting molten plastic into a mold cavity.
- Blow Molds: Designed for hollow plastic products such as bottles and containers.
- Compression Molds: Commonly used for thermosetting polymers where heat is applied to form the plastic shape.
- Rotational Molds: Suitable for large hollow shapes and objects.
- Thermoforming Molds: Used for softening plastic sheets and forming them into specific shapes.
The Impact of Technological Advancements
With the advancement of technology, the role of a plastic mold maker has evolved dramatically:
3D Printing and Prototyping
3D printing has revolutionized mold making by allowing rapid prototyping. This process allows designers to quickly iterate designs and make necessary adjustments long before production begins. This significantly reduces time and costs associated with mold production.
Computer-Aided Design (CAD)
Modern mold makers employ advanced CAD software that enables intricate and precise design features. By utilizing CAD, mold makers can simulate the injection process and foresee potential design flaws, thus streamlining the production process.
Smart Manufacturing
The integration of smart technologies, such as IoT and AI, into the manufacturing process allows mold makers to achieve better monitoring and predictive maintenance, improving efficiency and reducing downtime.
Challenges Faced by Plastic Mold Makers
While the role of a plastic mold maker is crucial, it is not without challenges:
- Material Limitations: Selecting the right material for molds can be a complex decision impacted by the end-use of the component.
- Market Competition: The global market for plastic products is competitive, demanding cost-effective and innovative solutions.
- Technological Changes: Keeping up with rapid technological advancements requires constant learning and adaptation.
- Environmental Concerns: As sustainability remains a top priority, mold makers must consider eco-friendly practices and materials.
The Future of Plastic Mold Making
The future for plastic mold makers looks promising, as the industry continues to advance and adapt to new technologies and consumer demands. Potential trends include:
Sustainability and Eco-Friendly Practices
As environmental sustainability becomes increasingly important, plastic mold makers will need to integrate eco-friendly materials and processes into their operations.
Enhanced Customization
With advancements in manufacturing technology, the capability for personalized and custom molds will expand, catering to niche markets and specialized products.
Integration of Advanced Robotics
Robotic automation in mold manufacturing can lead to enhanced accuracy and efficiency, reducing manual labor and human error.
Conclusion
The role of a plastic mold maker is vital in the manufacturing industry. From designing complex molds to producing high-quality plastic products, the expertise and innovation offered by mold makers drive the success of diverse industries. Companies like hanking-mould.com are at the forefront of this transformation, continuously enhancing their processes through technological advancements and superior craftsmanship.
Investing in skilled plastic mold makers today will pave the way for successful manufacturing solutions tomorrow.